Preventing Weld Undercut: Proven Techniques Every Welder Should Know
Preventing Weld Undercut: Proven Techniques Every Welder Should Know
Blog Article
Understanding the Art of Welding: Exactly How to Avoid Undercut Welding Issues for Flawless Construction Results
By comprehending the origin causes of undercut welding and executing efficient strategies to prevent it, welders can raise their craft to new levels of quality. In the search of perfect construction outcomes, understanding the art of welding to stay clear of undercut problems is not just an ability however a requirement for those aiming for excellence in their job.
Understanding Undercut Welding

To prevent undercut welding, welders need to guarantee correct welding parameters, such as adjusting the existing, voltage, travel speed, and maintaining the right electrode angle. By comprehending the reasons of undercut welding and executing precautionary actions, welders can attain high-grade, structurally sound welds.
Root Causes Of Undercut in Welding
Understanding the elements that add to undercut in welding is necessary for welders to produce high-grade, structurally audio welds. Damaging happens when the weld metal does not correctly fill up the groove developed between the base steel and the previously deposited weld metal. A number of factors can lead to damage in welding. One usual cause is excessive heat input. Welding at high temperatures for extended durations can lead to the base steel thawing even more than preferred, bring about damage. Insufficient welding wrong or present welding rate can also add to damage. Inadequate current might not offer enough warmth to thaw the base and filler metals effectively, while excessive rate can stop appropriate combination, causing undercut. In addition, improper electrode angles or incorrect torch control methods can develop locations of reduced weld steel deposition, advertising undercut. Comprehending these causes and implementing correct welding methods can help stop undercutting concerns, making sure durable and strong welds.
Methods to Prevent Undercutting

To alleviate the threat of damaging in welding, welders can utilize calculated welding techniques aimed at boosting the high quality and integrity of the weld joints. Additionally, using the correct welding method for the certain joint arrangement, such as weave or stringer beads, can contribute to decreasing damaging.
Moreover, proper joint prep work, consisting of ensuring tidy base products without pollutants and utilizing the suitable welding consumables, is crucial in preventing undercut defects. Utilizing back-step welding techniques and managing the weld bead profile can likewise aid disperse heat evenly and lessen the threat of undercut. Normal examination of the weld joint throughout and after welding, as well as carrying out quality control steps, can assist in attending to and detecting damaging concerns without delay. By executing these methods faithfully, welders can accomplish perfect manufacture results with minimal undercut problems.
Value of Appropriate Welding Parameters
Selecting and maintaining appropriate welding criteria is crucial for accomplishing effective welds with very little issues. Welding criteria describe variables such as voltage, current, travel speed, electrode angle, and protecting gas circulation rate that directly impact the welding procedure. These criteria should be very carefully changed based upon the sort of product being welded, its thickness, and the welding technique employed.
Appropriate welding parameters guarantee the correct amount of warm is put on melt the base metals and filler product evenly. If the criteria are set expensive, it can cause excessive warm input, creating spatter, burn-through, or distortion. On the various other hand, if the criteria are as well reduced, insufficient blend, lack of infiltration, or damaging may occur.
Quality Control in Welding Procedures
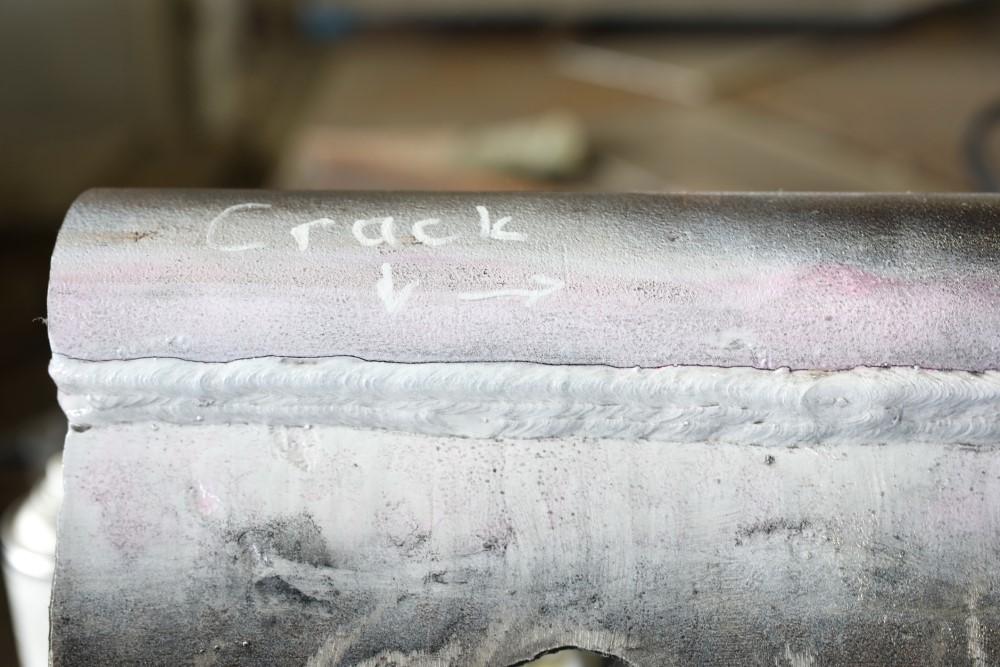
Verdict
Finally, understanding the art of welding needs a comprehensive understanding of undercut welding, its causes, and techniques to stop it. By making sure appropriate welding criteria and implementing high quality guarantee practices, flawless fabrication outcomes can be attained. It is important for welders to constantly pursue excellence in their welding operations to avoid undercut issues and produce top notch welds.
Undercut welding, a common problem in welding processes, occurs when the weld steel does not appropriately load the groove and leaves a groove or clinical depression along the bonded joint.To prevent undercut welding, welders should make certain correct welding specifications, such as readjusting the existing, voltage, travel rate, and maintaining the proper electrode angle. Insufficient welding present or incorrect welding speed look these up can additionally add to damage.To minimize the risk of damaging in welding, welders can utilize calculated welding strategies intended at improving the top quality and integrity of the weld joints.In final thought, mastering the art of welding requires a thorough understanding of undercut welding, its reasons, and methods to avoid it.
Report this page